การผลิตแบบลีนช่วยให้คุณปรับกระบวนการทางธุรกิจทั้งหมดในองค์กรให้เหมาะสม มุ่งเป้าไปที่การลดต้นทุน การเปิดตัวกระบวนการผลิตที่ต่อเนื่อง โดยเน้นที่ผู้ใช้ปลายทาง
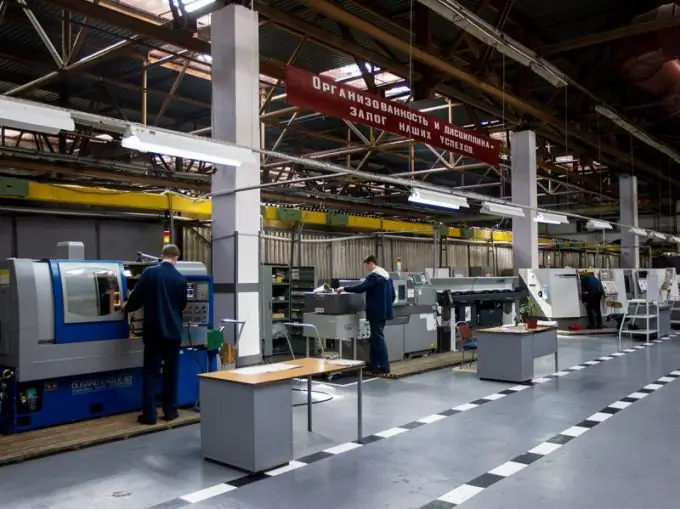
หลักการแบบลีนมักใช้ในองค์กรเพื่อลดต้นทุน ด้วยความช่วยเหลือของพวกเขา สามารถลดจำนวนการดำเนินการที่ไม่สามารถเพิ่มมูลค่าของผู้บริโภคในกระบวนการผลิตได้
การผลิตแบบลีนหมายถึงแผนการจัดการพิเศษสำหรับบริษัท แนวคิดหลักคือการพยายามลดค่าใช้จ่ายใดๆ ให้รวมพนักงานแต่ละคนไว้ในขั้นตอนการเพิ่มประสิทธิภาพ โครงการดังกล่าวมุ่งสู่ผู้บริโภคอย่างสมบูรณ์
ประวัติศาสตร์
ผู้ก่อตั้งแนวคิดคือ Taiichi Ohno ผู้พัฒนาหลักการพื้นฐาน เขาทำงานให้กับ Toyota Motor Co ตั้งแต่ปี 1943 ในปี ค.ศ. 1945 ญี่ปุ่นแพ้สงคราม เพื่อเอาชีวิตรอดในภาวะถดถอย จึงจำเป็นต้องมีแนวทางใหม่ในการแก้ไขปัญหา ในช่วงหลายปีที่ผ่านมา อเมริกาเป็นผู้นำในอุตสาหกรรมยานยนต์อย่างไม่มีข้อโต้แย้ง เป็นเวลาหลายปีที่มีการลดต้นทุนด้วยการเพิ่มการผลิตจำนวนมาก สไตล์นี้ใช้ได้กับทุกพื้นที่อย่างรวดเร็ว
ประธานบริษัท Toyota Motor Co กล่าวว่าจำเป็นต้องติดต่อกับอเมริกาภายใน 3 ปี หากยังไม่เสร็จสิ้น อุตสาหกรรมยานยนต์ในญี่ปุ่นก็ไม่อาจอยู่รอดได้ ดังนั้นจึงใช้ความพยายามทั้งหมดในการพัฒนาระบบการผลิตของตนเอง ซึ่งแตกต่างจากระบบการผลิตจำนวนมากแบบเดิมของญี่ปุ่น ในเวลาเดียวกัน เป้าหมายไม่ได้บรรลุโดยการขยายพื้นที่การผลิต แต่โดยการผลิตรถยนต์ในจำนวนน้อยตามโครงการใหม่
ปัจจัยสำคัญคือการพึ่งพาปัจจัยมนุษย์และการสร้างบรรยากาศของการช่วยเหลือซึ่งกันและกัน หลักการใหม่ที่นำมาใช้ไม่เพียงแต่ใช้กับพนักงานเท่านั้น แต่ยังรวมถึงลูกค้าและซัพพลายเออร์ด้วย ในอีก 15 ปีข้างหน้า ญี่ปุ่นมีการเติบโตทางเศรษฐกิจอย่างรวดเร็วผิดปกติ
คุณสมบัติและหลักการ
ประเด็นหลักคือการประเมินมูลค่าของผลิตภัณฑ์ที่ผลิตขึ้นสำหรับผู้บริโภคเฉพาะราย สถานการณ์ถูกสร้างขึ้นซึ่งมีการกำจัดความสูญเสียอย่างต่อเนื่อง ทำให้สามารถลบการดำเนินการที่ใช้ทรัพยากรได้ แต่ไม่ก่อให้เกิดค่า Taiichi Ohno ระบุการสูญเสียหลายประเภท:
- เนื่องจากการผลิตมากเกินไป
- รอเวลา;
- การขนส่งที่ไม่จำเป็น
- ขั้นตอนการประมวลผลที่ไม่จำเป็น
- การก่อตัวของสต็อกส่วนเกิน
- การเคลื่อนไหวของวัตถุโดยไม่จำเป็น
- การเกิดขึ้นของสินค้าที่บกพร่อง
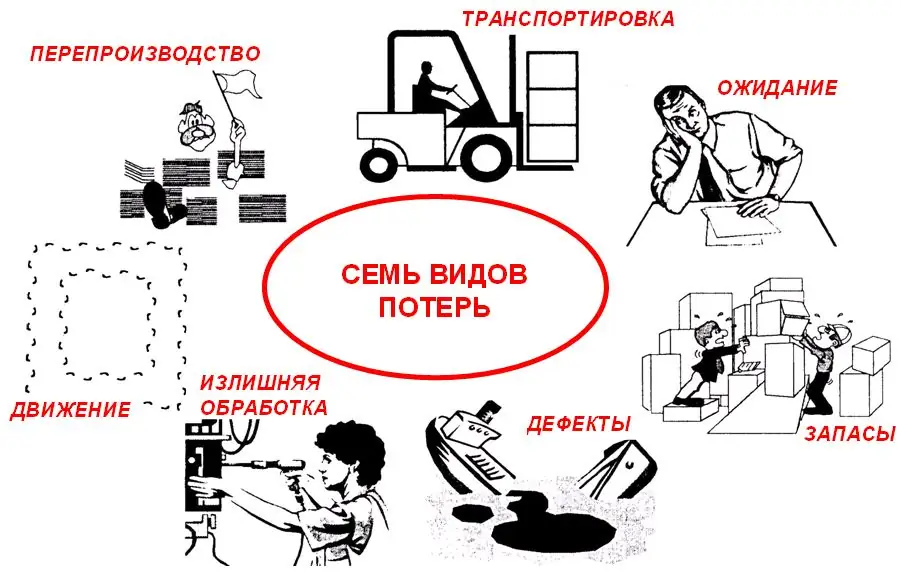
หมายถึงประเภทของการสูญเสียและประสิทธิภาพการทำงานที่ไม่สม่ำเสมอ สิ่งนี้เกิดขึ้น เช่น กับตารางการทำงานที่ไม่ต่อเนื่องขององค์กรอันเนื่องมาจากอุปสงค์ที่ผันผวนในตลาดผู้บริโภค
ในการนำการผลิตแบบลีนมาใช้นั้น ไม่เพียงแต่จำเป็นต้องคำนวณการสูญเสียเท่านั้น แต่ยังต้องนำหลักการพื้นฐานไปใช้ สมมติฐานแรก: คุณต้องกำหนดสิ่งที่สร้างมูลค่าของผลิตภัณฑ์จากมุมมองของผู้บริโภค บางครั้งมีการจัดการจำนวนมากในองค์กร ซึ่งกลายเป็นว่าไม่สำคัญต่อผู้มีโอกาสเป็นลูกค้า แนวทางนี้จะช่วยให้คุณสามารถกำหนดได้ว่ากระบวนการใดมุ่งเน้นไปที่การให้คุณค่าและกระบวนการใดไม่ได้
หลักการที่สองมีจุดมุ่งหมายเพื่อระบุประเด็นสำคัญในห่วงโซ่การผลิตทั้งหมดและกำจัดของเสีย สำหรับสิ่งนี้ การดำเนินการทั้งหมดจะอธิบายโดยละเอียดตั้งแต่ช่วงเวลาที่ได้รับคำสั่งซื้อ ไปจนถึงการโอนผลิตภัณฑ์ไปยังผู้ซื้อโดยตรง วิธีนี้ช่วยให้คุณระบุสิ่งที่จำเป็นในการเพิ่มประสิทธิภาพการทำงานและกระตุ้นการผลิตได้
หลักการที่สามเกี่ยวข้องกับกิจกรรมการปรับโครงสร้างเพื่อแสดงถึงเวิร์กโฟลว์ แง่มุมนี้ถือว่าต้องดำเนินการทั้งหมดเพื่อไม่ให้มีการหยุดทำงานระหว่างกัน บางครั้งด้านนี้จำเป็นต้องมีการแนะนำเทคโนโลยีใหม่จากนั้นกระบวนการทั้งหมดจะประกอบด้วยการกระทำที่ส่งผลดีต่อตัวผลิตภัณฑ์เอง
หลักการที่สี่คือความจำเป็นในการดำเนินการที่จำเป็นสำหรับผู้บริโภคเอง องค์กรควรผลิตสินค้าเท่าที่จำเป็นเท่านั้น
หลักการข้อที่ห้าคือความจำเป็นในการปรับปรุงอย่างต่อเนื่องโดยลดการกระทำที่ไม่จำเป็น การนำระบบไปใช้จะไม่ทำงานหากใช้หลักการเป็นครั้งคราวเท่านั้น หากคุณตัดสินใจที่จะเริ่มใช้งานระบบ คุณต้องดำเนินการนี้อย่างต่อเนื่อง
เครื่องมือลีน Le
ช่วยให้ใช้หลักการแบบลีนได้ง่ายขึ้น เครื่องมือถูกนำไปใช้เป็นรายบุคคลและรวมกัน ซึ่งรวมถึง:
- การจัดพื้นที่ที่เหมาะสม ความเข้าใจในปัญหาที่เกิดขึ้น การตรวจจับความเบี่ยงเบนต่างๆ
- ระบบแจ้งปัญหา. จะได้รับสัญญาณพิเศษ อนุญาตให้หยุดการผลิตเพื่อป้องกันไม่ให้เกิดข้อบกพร่องจำนวนมาก
- การจัดตำแหน่งสตรีมโดยไม่มีการหยุดชะงักและการสะสมบัฟเฟอร์ เครื่องมือนี้ทำให้สามารถขจัดความสูญเสียประเภทต่างๆ ได้ตั้งแต่หุ้นส่วนเกิน
- สิ่งสำคัญที่สุดไม่ได้เกิดขึ้นที่สำนักงาน แต่อยู่ในสถานที่ผลิต การมีส่วนร่วมของฝ่ายบริหารช่วยลดเวลาตอบสนองเมื่อเกิดปัญหาขึ้น มีการเสริมสร้างวินัยและข้อมูลโดยตรง
- มีการตรวจสอบประสิทธิภาพโดยรวมของอุปกรณ์อยู่เสมอ เครื่องมือนี้ติดตามการสูญเสียอุปกรณ์สามประเภท: ความพร้อมใช้งาน ประสิทธิภาพ และคุณภาพ
มีเครื่องมือการผลิตแบบลีนอื่นๆ ซึ่งทั้งหมดมุ่งเป้าไปที่ความโปร่งใสของกระบวนการจัดการ ลดต้นทุนด้านคุณภาพผลิตภัณฑ์ และเพิ่มการมีส่วนร่วมของพนักงานในกระบวนการผลิต
คุณสมบัติของวิธีการผลิตแบบลีน
แนวคิดนี้เข้าใจง่าย แต่ยากที่จะนำไปปฏิบัติได้จริง บ่อยครั้ง การนำหลักการไปปฏิบัติต้องมีการเปลี่ยนแปลงในวัฒนธรรมทั้งหมดของบริษัท ซึ่งอาจต้องใช้เวลาเท่านั้น แต่ยังต้องใช้เงินด้วย แนวคิดนี้เน้นที่การพิจารณาผลประโยชน์สูงสุดของลูกค้าและผู้บริโภค องค์กรระดับสูงของกระบวนการทั้งหมดช่วยให้คุณหลีกเลี่ยงค่าใช้จ่ายที่ไม่จำเป็นและแข่งขันในตลาดสมัยใหม่
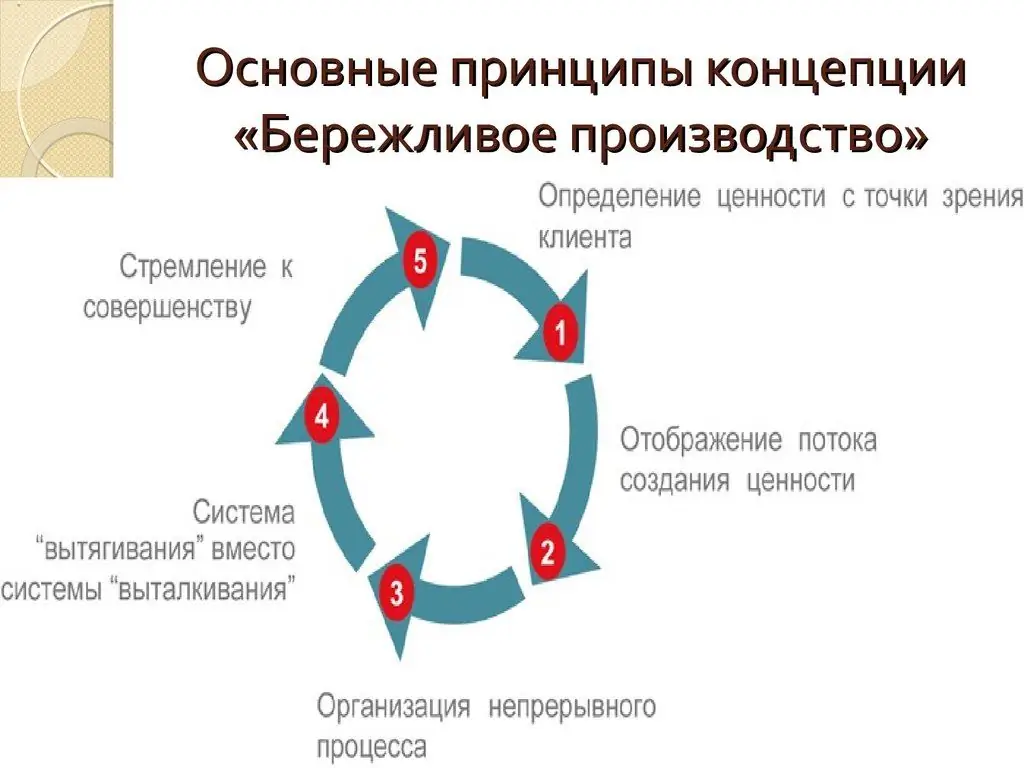
ประสบการณ์โลกแสดงให้เห็นว่าการดำเนินการตามหลักการที่อธิบายไว้:
- เพิ่มผลิตภาพแรงงาน 35-70%;
- ลดเวลาวงจรการผลิตลง 25-90%;
- ลดความเป็นไปได้ของการแต่งงานลง 59-98%;
- เพิ่มคุณภาพของผลิตภัณฑ์ขึ้น 40%
หลักการแบบลีนสามารถนำไปใช้ได้หลากหลายด้าน ประเด็นเหล่านี้มีความเกี่ยวข้องอย่างยิ่งในด้านการผลิต การขนส่ง การธนาคาร การค้า การสร้างเทคโนโลยีสารสนเทศ การก่อสร้าง และบริการทางการแพทย์
การดำเนินการตามหลักการเกิดขึ้นในสามขั้นตอน ประการแรกมีการศึกษาความต้องการ ด้วยเหตุนี้จึงใช้การคำนวณระยะพิทช์ เวลาแท็ค และเทคโนโลยีพิเศษอื่นๆ ในขั้นตอนที่สอง ความต่อเนื่องของกระแสคุณค่าจะทำสำเร็จ มีการดำเนินมาตรการบางอย่างที่ทำให้สามารถจัดหาผลิตภัณฑ์ให้ผู้บริโภคได้ทันเวลาและในปริมาณที่เหมาะสม ในขั้นตอนที่สาม การปรับให้เรียบจะเกิดขึ้นเมื่อมีการกระจายปริมาณและงานที่ทำอย่างสมดุล
การดำเนินการจะประสบความสำเร็จหากใช้เครื่องมือและทรัพยากรอย่างครบถ้วนในกระบวนการ และแผนการฝึกอบรมและคุณสมบัติของพนักงานได้รับการอนุมัติแล้ว อย่างหลังมีความสำคัญ เนื่องจากเมื่อทำงานในบริษัท ผู้คนมักจะได้รับเชิญที่มีความรู้ ทักษะ และประสบการณ์ที่แตกต่างกัน คุณสามารถเรียนรู้จากประสบการณ์ทั้งการใช้โปรแกรมการฝึกอบรมพิเศษและการสังเกตเพื่อนร่วมงาน
นอกจากนี้ การผลิตแบบลีนยังเกี่ยวข้องกับการพัฒนาความคิดสร้างสรรค์ในพนักงานแนวทางนี้ช่วยให้คุณก้าวไปไกลกว่าองค์กรใดองค์กรหนึ่งเพื่อทำงานอย่างมีประสิทธิภาพในทุกทิศทาง พนักงานทุกคนจะต้องสามารถค้นหาวิธีแก้ไขปัญหาที่แตกต่างกันในสถานการณ์เดียวกันได้